Visual inspection carrier equipment, a device used to perform visual inspection on a production line for the automated inspection and sorting of electronic components, components or products. The combination of conveyor systems, cameras, light sources and image processing software enables continuous and efficient inspection and classification of products.
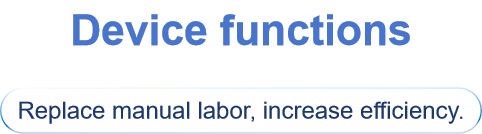
Detect defect
Visual inspection belt equipment can detect surface defects of products, such as missing, damage, foreign bodies, etc.
Location recognition
Through the vision system, the device can accurately identify the location and orientation of the on-board components or products, which helps in subsequent processing and treatment.
Counting and sorting
Visual inspection belt equipment can count and classify products to help automate production and management of production lines.
Data recording
The equipment can record test results, counting information and other data to support statistical analysis of production data and quality management.
Alarm and exclusion
When abnormal conditions or defects are detected, the equipment can send an alarm signal and implement corresponding exclusion measures to ensure the stability and reliability of the production process.
Automated production
Automated production line integration to achieve automatic detection and processing of components or products in the production process, improve production efficiency and product quality.
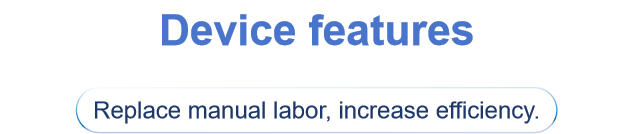
Device model: SP-800 series
Machine features: Special hardware device visual inspection carrier platform
Main functions: detection of leakage, reverse, vertical measurement, mixing, up to five simultaneous detection
Scope of application: Suitable for all kinds of hardware, electronic parts, plastic parts, belt packaging
Detection accuracy: Accuracy up to 0.01mm
Detection efficiency: up to 500 PCS/min
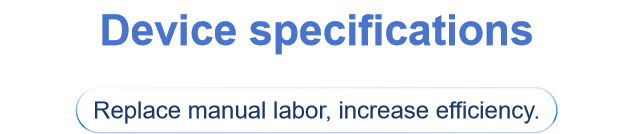
Device type | Visual inspection carrier equipment |
Scope of application | It is suitable for the detection of rubber parts, precision hardware parts, automobile, mobile phone parts, plastic parts, electronic parts and other high-precision products. |
Optical system | Germany high rate CCD industrial camera, Japan imported lens, professional light source system |
Number of cameras | Standard 1 (can be configured according to demand) |
Control system | Germany Siemens Industrial Computer |
Image detection software | Siptech Vision inspection System |
Feed system | Conveyor belt |
Detection speed | 60 ~ 300 PCS/min (depending on product size) |
Recommended inspection size | 30 ~ 200mm |
Detection quality | 5 ~ 500g |
precision | Up to ±0.01mm |
Detection index | Detection of missing, misloading, mixing, defect detection, size detection, screen printing detection, etc |
Supply voltage | Two-phase 220V, 50Hz |
Rated power | 1kW |
Atmospheric pressure | The air pressure is not less than 0.35 ~ 0.7MPa |
Equipment weight | Approx. 150kg |
Operating temperature | -3 ° C to 45 ° C |
Storage temperature | -20℃ ~ 60℃ |
Equipment size | 1900mm(L)×500mm(W)×1300mm(H) |
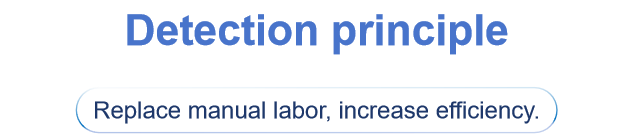
Conveyor belt system: The carrier belt transmits the product along the set path to the detection area through the conveyor belt system.
Image acquisition: The camera captures the image of the product surface and transmits it to the image processing system for processing.
Light source Settings: The right light source Settings can provide good lighting conditions and ensure image clarity and contrast.
Image processing: The image processing software analyzes the captured images and detects the features of the product, such as defects, marks, dimensions, etc.
Detection and classification: According to the preset detection algorithm, the product is detected and classified to determine whether it meets the quality standard.
Sorting and processing: According to the test results, the product is classified into qualified products and unqualified products, and the corresponding sorting or processing mechanism is triggered.
Real-time monitoring: The equipment usually has a real-time monitoring function, which can monitor the detection of products on the production line and find problems in time.
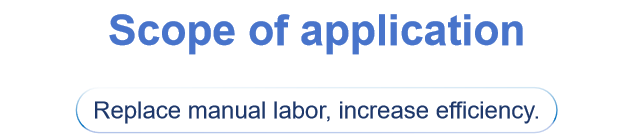
Electronic manufacturing: used to detect the welding quality, size, position, etc., of electronic components.
Auto parts: It can be used to test the appearance quality and assembly accuracy of auto parts.
Medical devices: Used to test the assembly quality and integrity of medical devices.
Food packaging: can be used to test the integrity of food packaging and label attachment.
Visual inspection equipment can improve the automation of the production line, reduce manual intervention, improve product quality and production efficiency, and reduce the cost loss caused by quality problems.
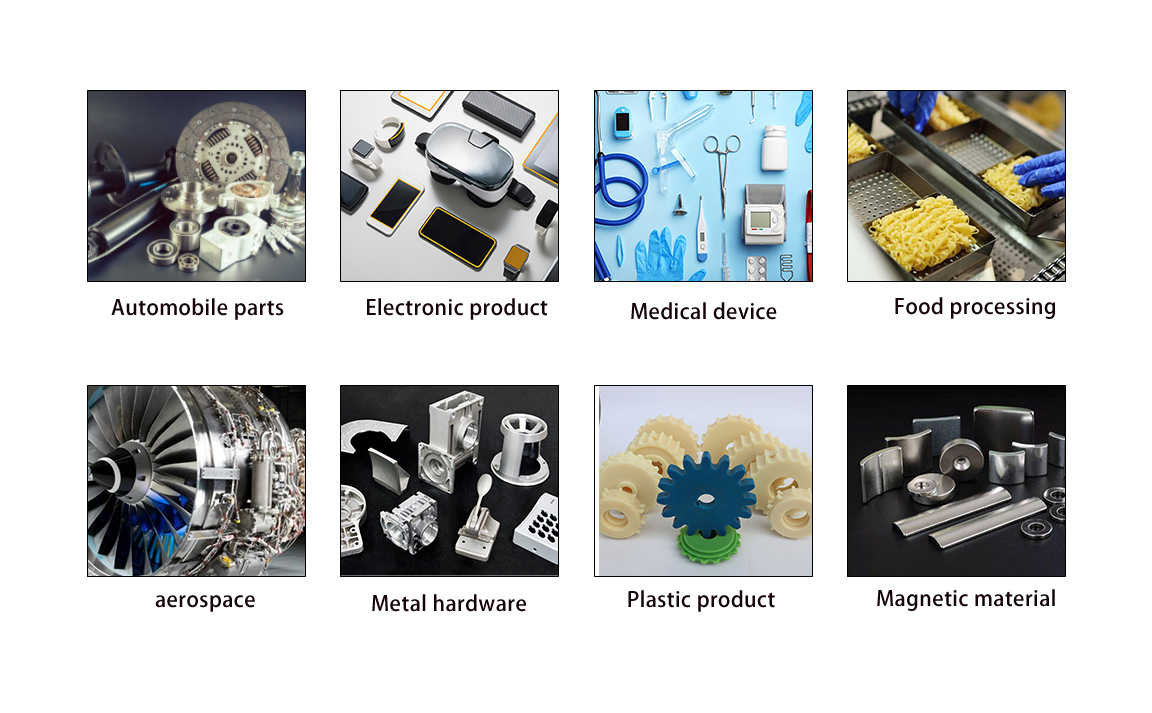